Indonesia Furniture Manufacturers for Dummies
Indonesia Furniture Manufacturers for Dummies
Blog Article
The Buzz on Indonesia Furniture Manufacturers
Table of ContentsThe 8-Second Trick For Indonesia Furniture ManufacturersThe Greatest Guide To Indonesia Furniture ManufacturersAll about Indonesia Furniture ManufacturersTop Guidelines Of Indonesia Furniture ManufacturersSome Ideas on Indonesia Furniture Manufacturers You Need To Know
There are some downsides to purchasing from a furnishings manufacturer. A furnishings seller is a company that offers furnishings made by various producers.When you purchase from a furniture retailer, you're getting a furniture piece that's currently been made and is all set to be shipped to your home. Among the advantages of purchasing from a furnishings merchant is that you can often see and touch the item prior to you acquire it.
At BH Furniture, we think in setting new standards for excellence in the production of industrial furniture - Indonesia furniture manufacturers. Our commitment to technology has led us to welcome cutting-edge automation innovation, transforming the means we manufacture furniture and pushing us to the leading edge of the market. Gone are the days of manual work controling the production flooring
Our equipment works seamlessly, assisted by the precise specifications established by our proficient engineers, ensuring consistently high-grade outcome. Bid farewell to manufacturing hold-ups and overtime prices. Our automated systems run tirelessly, 24/7, ensuring a stable and uninterrupted operations. This indicates we not just fulfill however surpass delivery deadlines, supplying our clients with a degree of dependability that conventional manufacturing approaches simply can't match.
Little Known Questions About Indonesia Furniture Manufacturers.
Our production capacity has soared, enabling us to meet the needs of also the largest jobs without endangering on high quality. As your companion in industrial furnishings options, we can effortlessly scale our outcome to suit your requirements, despite the scale. While conventional manufacturing relies greatly on manual work, our automated systems have actually substantially minimized our dependancy on a large labor force.
Furniture manufacturing is a complex process that involves different stages, from developing and product selection to manufacturing and assembly. At each phase, there is a possibility of flaws or mistakes that can compromise the quality of the end product. To make certain that furnishings is of premium quality, furniture manufacturers execute quality assurance procedures to identify and fix any type of issues that might occur throughout production.
The inspection procedure should cover various elements, such as assembly, surface, colour, design, packaging, labelling, and noting. By carrying out a rigorous assessment procedure, producers can guarantee their products fulfill the necessary high quality, safety, and longevity demands. They additionally provide the versatility to resolve problems and make improvements before completing the final product.
The procedure starts with the raw materials assessment to the last assembly of the furnishings. The goal is to make certain that the products are devoid of issues, secure, and satisfy the client's expectations. Furniture quality requirements are collections of standards and needs for furnishings production. They define the needed quality degree of furniture production and cover aspects such as safety and security, sturdiness, stamina, and ecological impact.
The 9-Second Trick For Indonesia Furniture Manufacturers

To ensure their furnishings products can sustain different weather components, including sunlight, rain, snow, and wind, manufacturers need to consider worldwide acknowledged criteria that make up evaluations and screening. Here are several of the standards to maintain in mind: ASTM F1561-03 is an international common developed by the American Area of the International Association for Testing Products (ASTM).
UL 962 is an international security requirement created by Underwriters Laboratories (UL), an independent global supply safety services business. The typical uses to household and commercial furnishings, including outside furniture.
Indonesia Furniture Manufacturers - An Overview
It helps to identify problems in the furniture and examine its performance and compliance with the called for top quality standards. Right here are the actions for performing laboratory testing for furniture: Producers collect examples of furniture parts that call for screening. These samples usually stand for the various sorts of furniture that they produce.
This may entail a combination of various tests, including stamina screening, resilience testing, safety screening, and ecological influence testing. The examples are after that tested for numerous high quality specifications, such as strength, sturdiness, security, and ecological effect. The results are then reviewed to establish whether the products satisfy the called for quality standards.
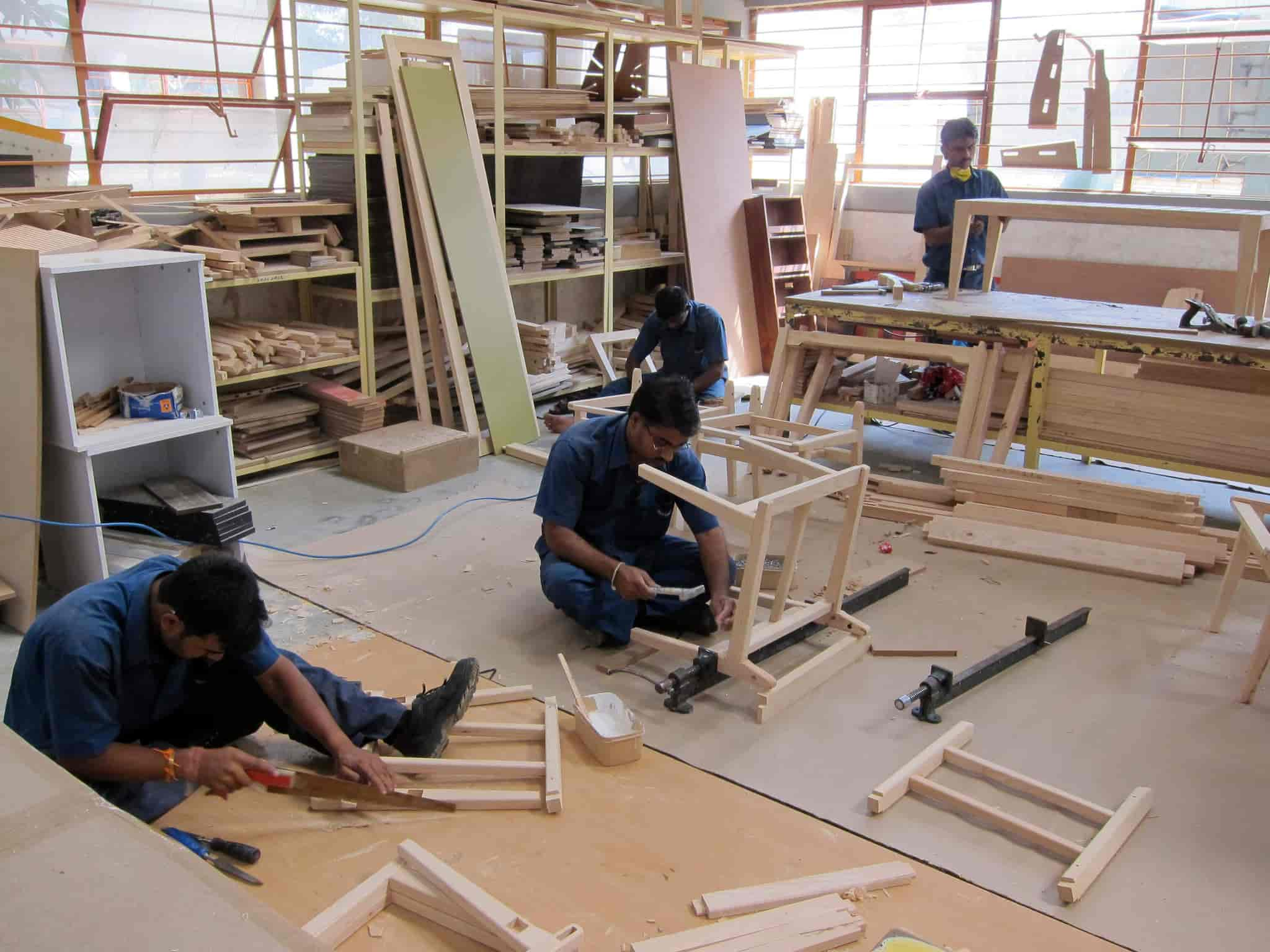
Normally, every retail store furniture is various. Layouts meeting customer benefit Maximizing room use in storage space, display, step, guest seating and pathways Ensuring ease of access to items for trials and acquisition Creating modular furniture that is simple to move and renovate Meeting security requirements of consumers A quick TAT from layout to production and installment with minimal errors can assist address the above worries.
The Indonesia Furniture Manufacturers Statements
A designer my company can understand the market patterns and be prepared with innovative styles ahead of time. Read below: How DriveWorks Assists You to Reduce Preparation in Production Designers usually have to transform the shapes and dimensions of furnishings at a moment's notification. These might have various visual and useful needs like front desk, and servicing workdesk that vary in measurements.
on an usual platform. This combination of sales and ERP features brings more exposure on price and pricing. It basically presents CPQ like performance and enables generating quick quotes and amounts for budget plan evaluations and settling orders. Indonesia furniture manufacturers. DriveWorks can auto-generate production shop drawings with BOMs and DXFs for sheet cutting and boxing

It is a very affordable market, with companies making every effort to keep up with altering customer demands and the newest technical trends. Today's consumers are a lot more most likely to favor furniture that is tailored and made with lasting materials.
Report this page